There will be a moment in time in almost every lathe owners’ career when the desire for a tool post grinder starts to grow.
I have a strong opinion on tool post grinders, and it’s not a good one.
The idea:
- Creating higher precision parts, possibly out of hardened materials
The reality:
- Grinding is not an inherent more precise process
- Grinding adds another layer of complexity
- Lathes are not designed to be a very good ID/OD grinder
- Tool post grinders are often quite crude devices. Very heavy and cumbersome to setup, often with belt drives that tend to add vibrations, motors sitting on top of a large stack up that add vibrations to the entire system
There are exceptions of course – Some materials just can not be cut with carbide/diamond or CBN inserts in a cost-effective manner. Ceramics and Carbide can be such a exception, also they have some utility when working with hard chrome plated items like hydraulic rods.
ID work in hardened steels or ceramic/carbides can be a case where grinding on the lathe is a viable solution, if no other machine is available.
But even then, it’s a good idea to keep the actual grinding done on the lathe to a minimum – I had to make some carbide bushings, to keep grinding to a minimum, I had the ID bore wire EDM cut to almost finished size, the OD of the stock was chosen to be the final dimension, and the length was ground on the surface grinder.
The actual grinding on the lathe was performed with a high-speed air driven spindle, held in a boring bar holder. This setup has some advantages over a classic tool post grinder, since it’s easy to setup.
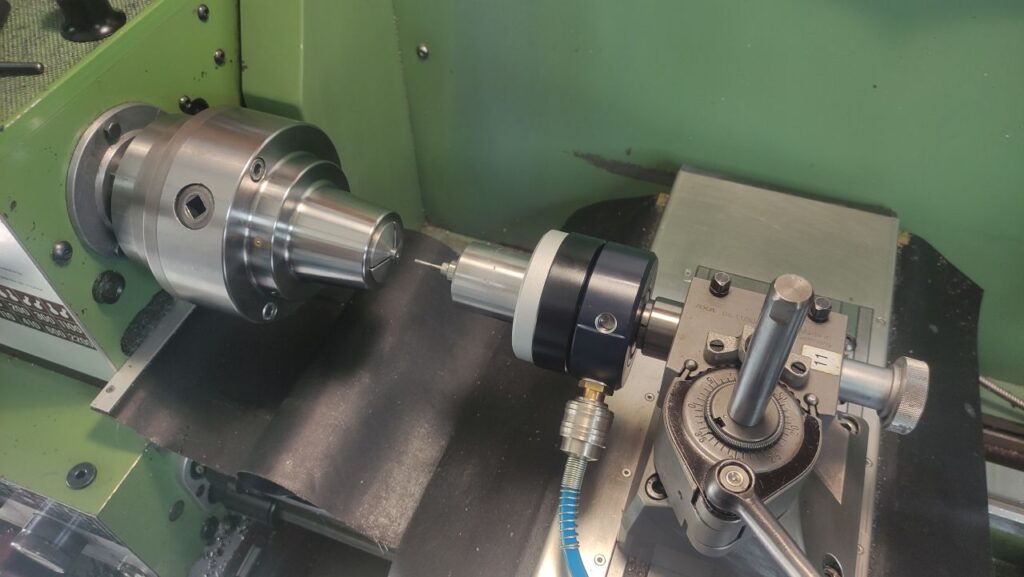
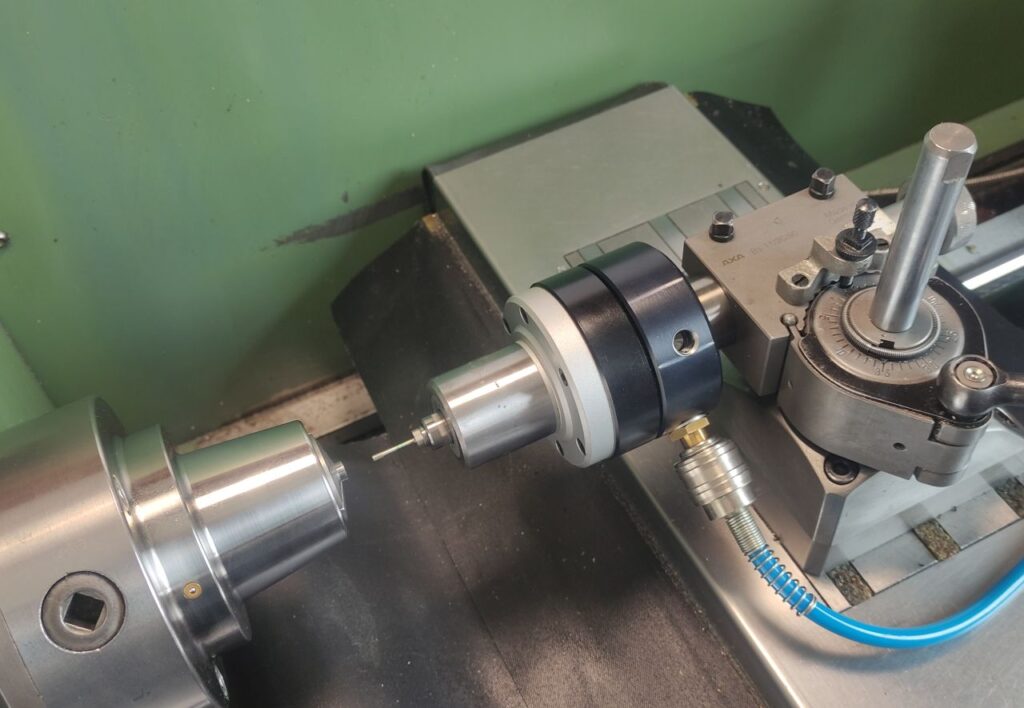
Most standard belt driven tool post grinders are too big to mount into a quick change tool post, they require to be bolted to the compound directly.