One thing that I noticed when learning about toolroom practices around the world – Europe tends to run separate ID/OD grinders for even very small and simple operations, while in the USA the surface grinder gets utilized as a universal platform for all sorts of grinding operations, including a fair share of round work.
For grinding round parts, you need a spindle to spin the work – The most well-known one is probably the Harig Grind-All. Also known as “Punch grinder”, “Punch former”, “Whirly Jig” or “Spin fixture”
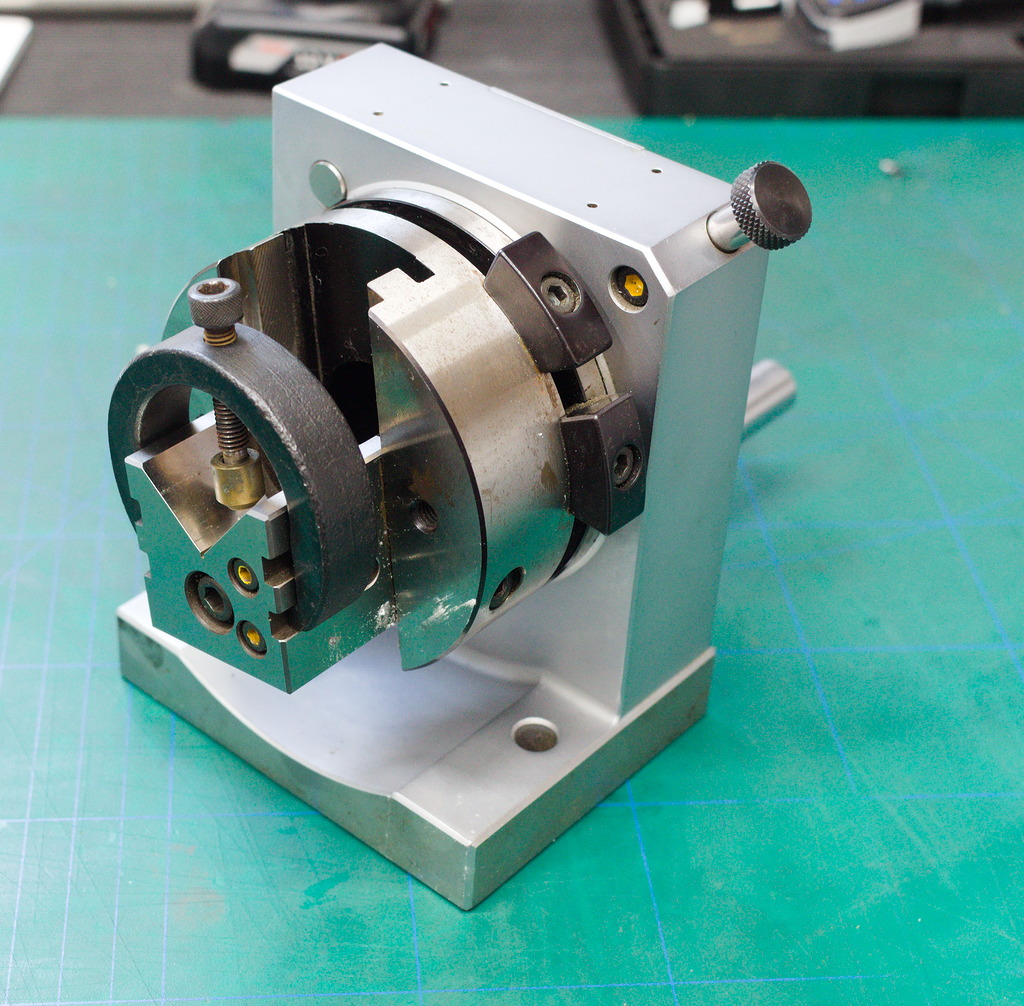
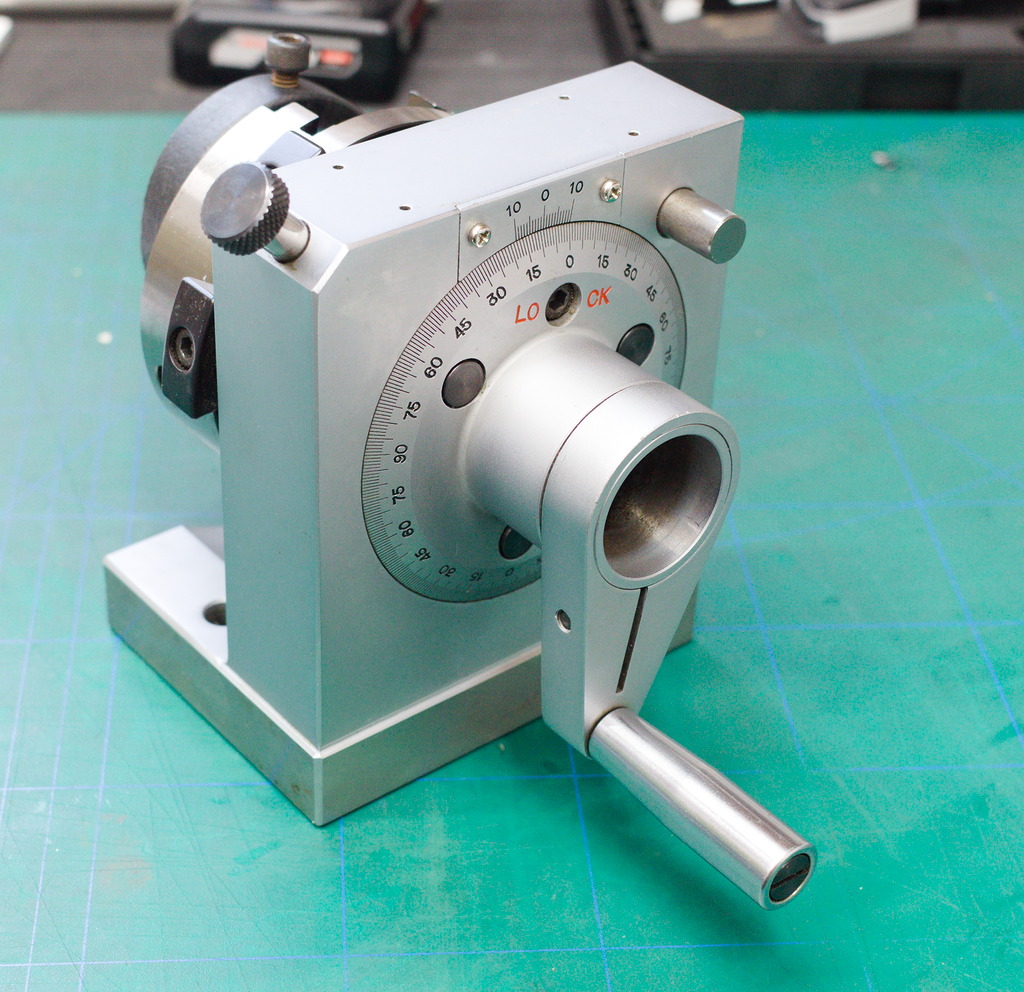
Assfalg400 Punch former with a sliding v-block
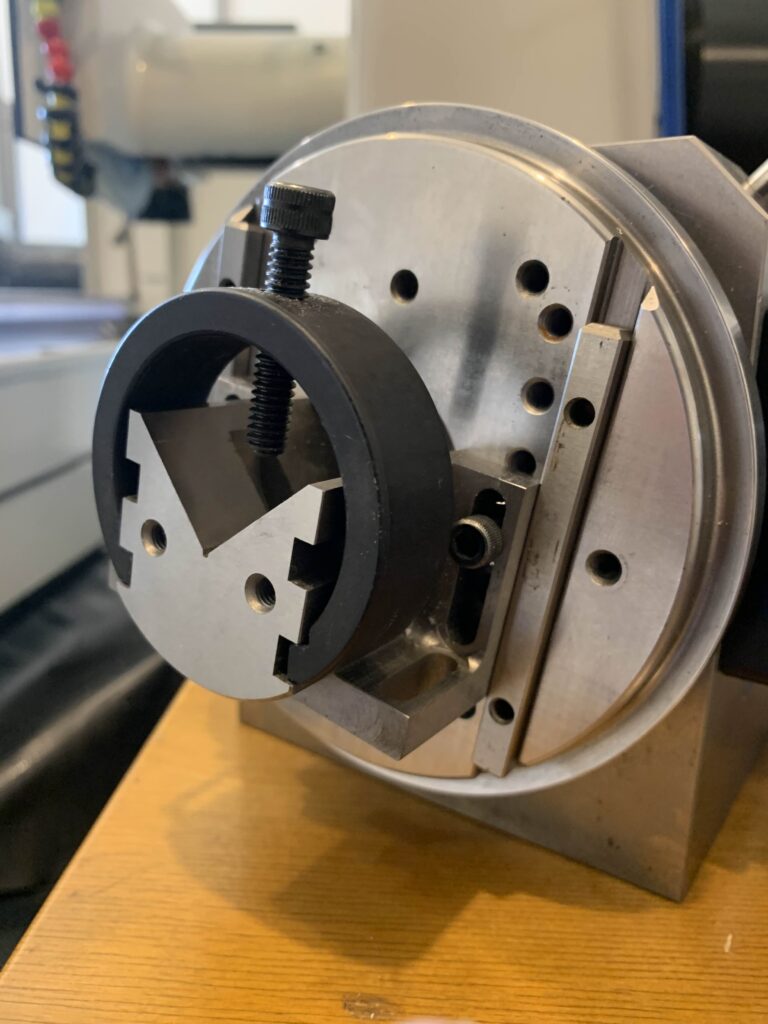
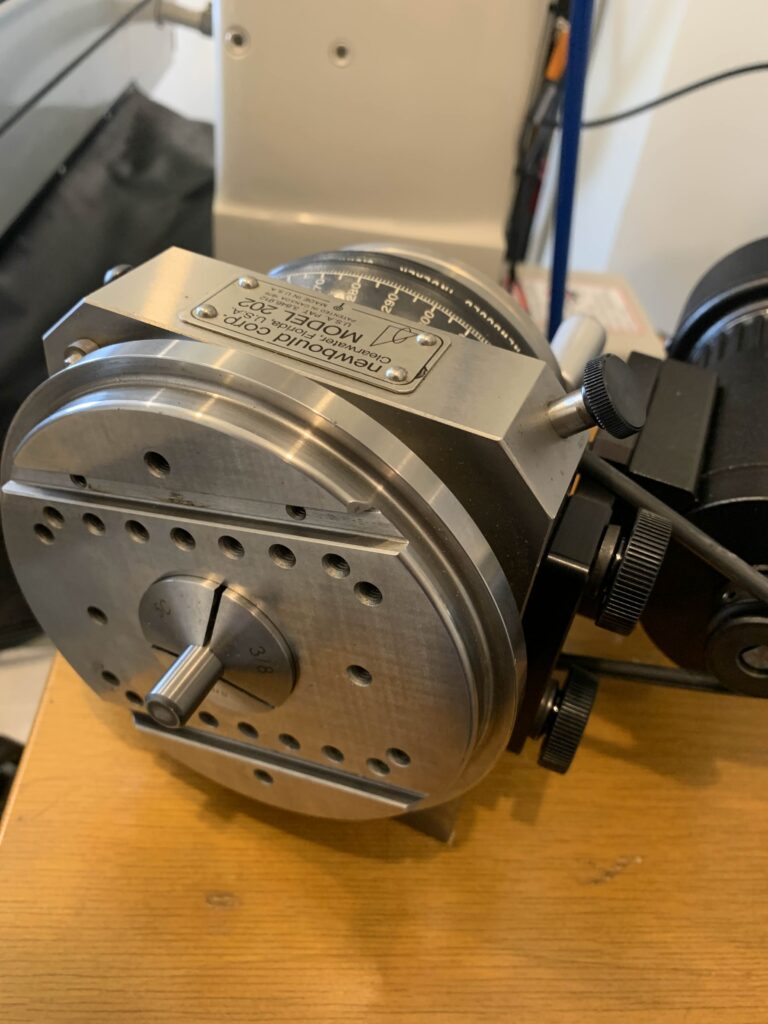
Newbould indexer with a sliding v-block and a 5C collet taper, when the v-block is removed.
(Picture by Adam Demuth)
These are fairly accurate devices that can be used for grinding round work, perform direct indexing, indexing via a vernier scale or indexing/segment indexing via adjustable stops.
Be aware, they are expensive tools, and they should be handled with care.
The earliest version of what we know today as a spin fixture can be found in a patent from 1946 – Still very crude:
https://patents.google.com/patent/US2449459A
A later patent, granted in 1960 shows already something that’s looking like the spin fixtures we can buy today – It also shows the bearing arrangement with the single row of balls running between beveled races, forming a four-point contact bearing.
https://www.datamp.org/patents/displayPatent.php?id=63980
https://patents.google.com/patent/US3094821
The basic Layout is always the same:
- A housing with a foot, usually meant to go onto a magnetic chuck.
- A short spindle, running in some means of ball bearings. Most designs use a single row of balls running on integral ball races.
- Work holding: Semi-Standard is a sliding V-Block to hold workpieces and adjust them to run true.
Options are 3 Jaw Chucks, ER Collets Chucks, integral Collet Tapers, Magnetic Chucks or integral zero-point systems like 3R or Erowa.
Systems with an integrated ER Collet chucks or 3 jaw chuck are in my opinion a very bad choice for general use, - Most have rotational stops that can be adjusted and integral 24 Position direct indexing with a shot pin.
Additional systems like the Newbould indexer exist, that allow for very accurate angle setting via differential face gears.
Adam demonstrates the face gear indexing in this Video:
Differential gear tooth indexing
https://youtu.be/3oE2axs0I5o?si=Pyjh15RAdjISfdT1
There is a modification to the sliding V-Block version, that allows a sliding motion in two axis – the second axis sliding motion is done via a rack/pinion drive from the backside of the spindle. This arrangement blocks the trough bore of the spindle, which makes it in my opinion less desirable for general work.
Some manufacturers/sellers call them one-way / two way punch formers.
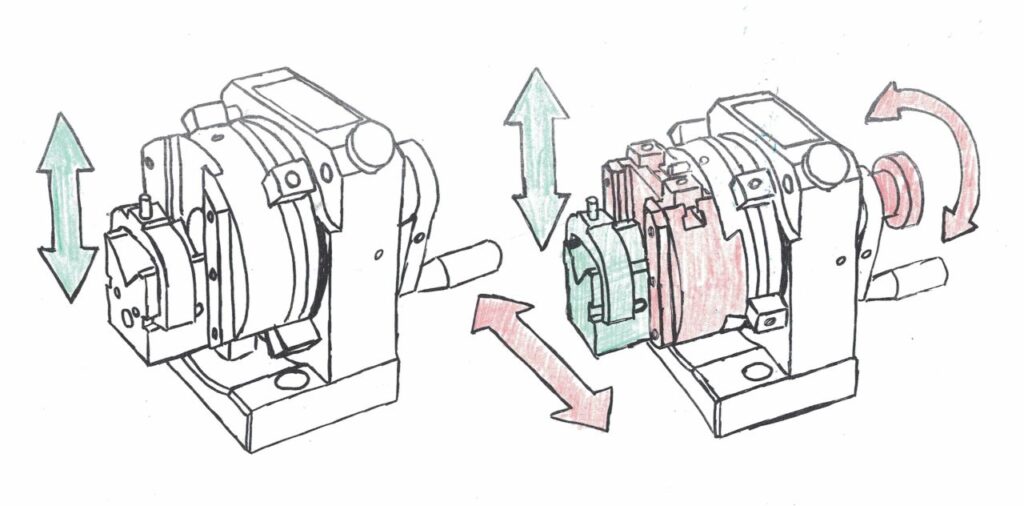
This second axis of motion allows to dress wheels at an angle with a diamond held in the V-Block or to create polygon shapes with corner radii offset in two axes.
Applications
- Grinding round/prismatic Workpieces
- Toolgrinding
- General indexing/rotary work
- Other
Examples of operation:
Tool grinding, ID threading tool:
Grinding a 55° threading tool out of a 8mm solid carbide blank.
All operations are performed using the spin fixture on the surface grinder. The neck of the tool is ground by putting the blank out of center, which is very easy to be done with the sliding v-block.
In general, the surface grinder with a magnetic chuck is a very powerful tool to grind tools, very often faster to setup than a real T&C grinder.
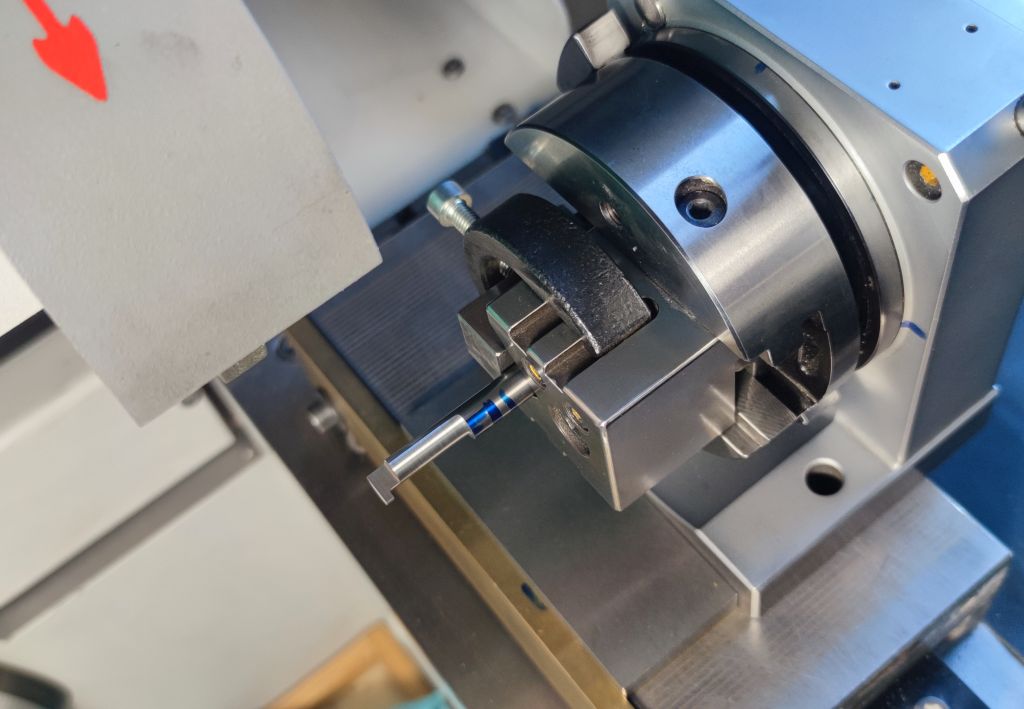
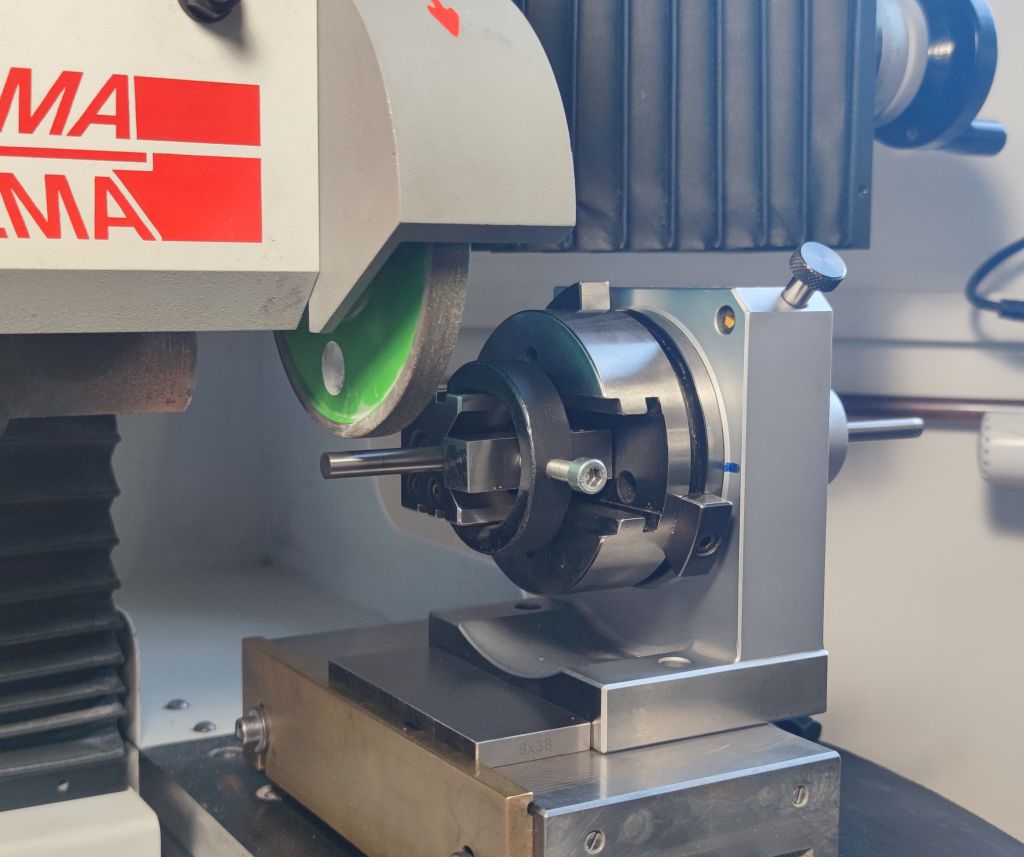
Grinding the excentric neck and splitting the cutting portion in half. The punch grinder is spaced off the fence with a parallel.
This is a recurring theme in using them – They are very universal, but with that universality comes some pain in getting them into a spot that allows you to access the part, not run out of machine travel and not to collide with anything.
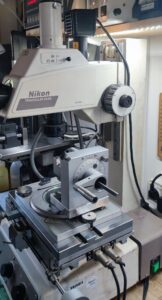
Since the spin fixture can be taken off the magnet and go back on very repeatable against the fence, it is easy to take it off, use whatever measuring instrument – like a toolmakers microscope – for inspection and go back to the grinder for adjustments.
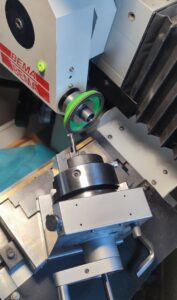
Angles can be set very easily with angle blocks against the fence.
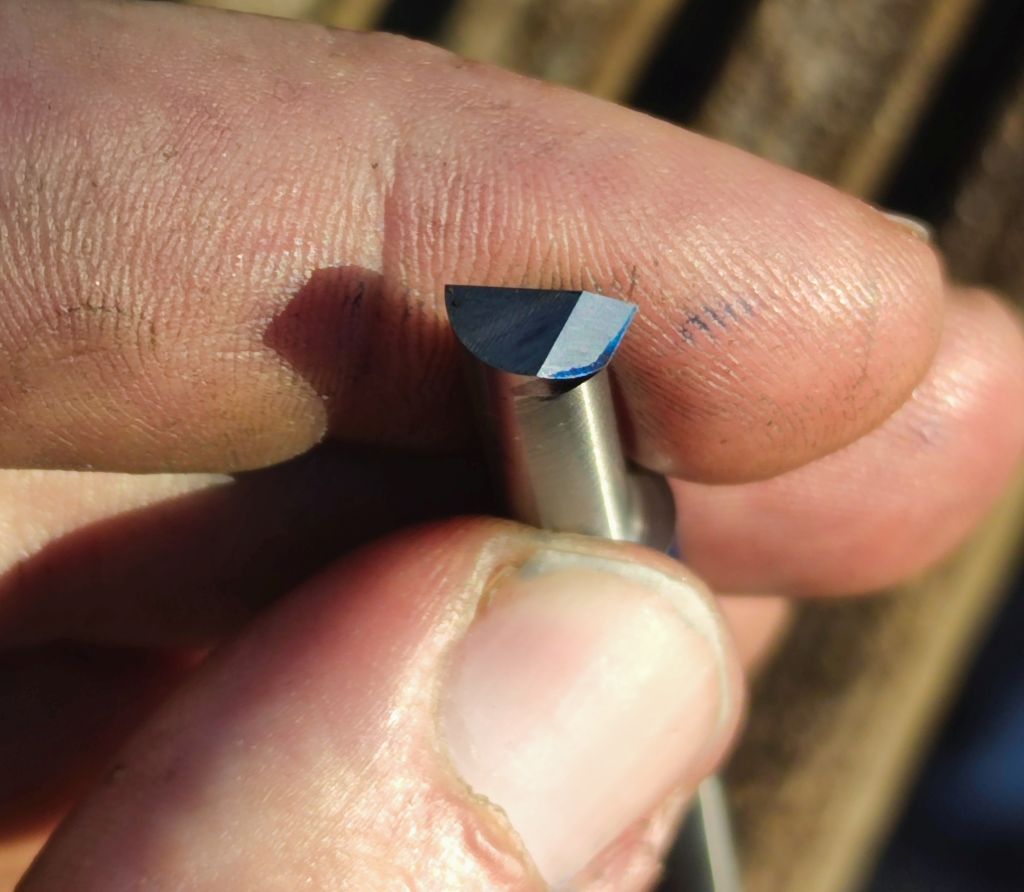
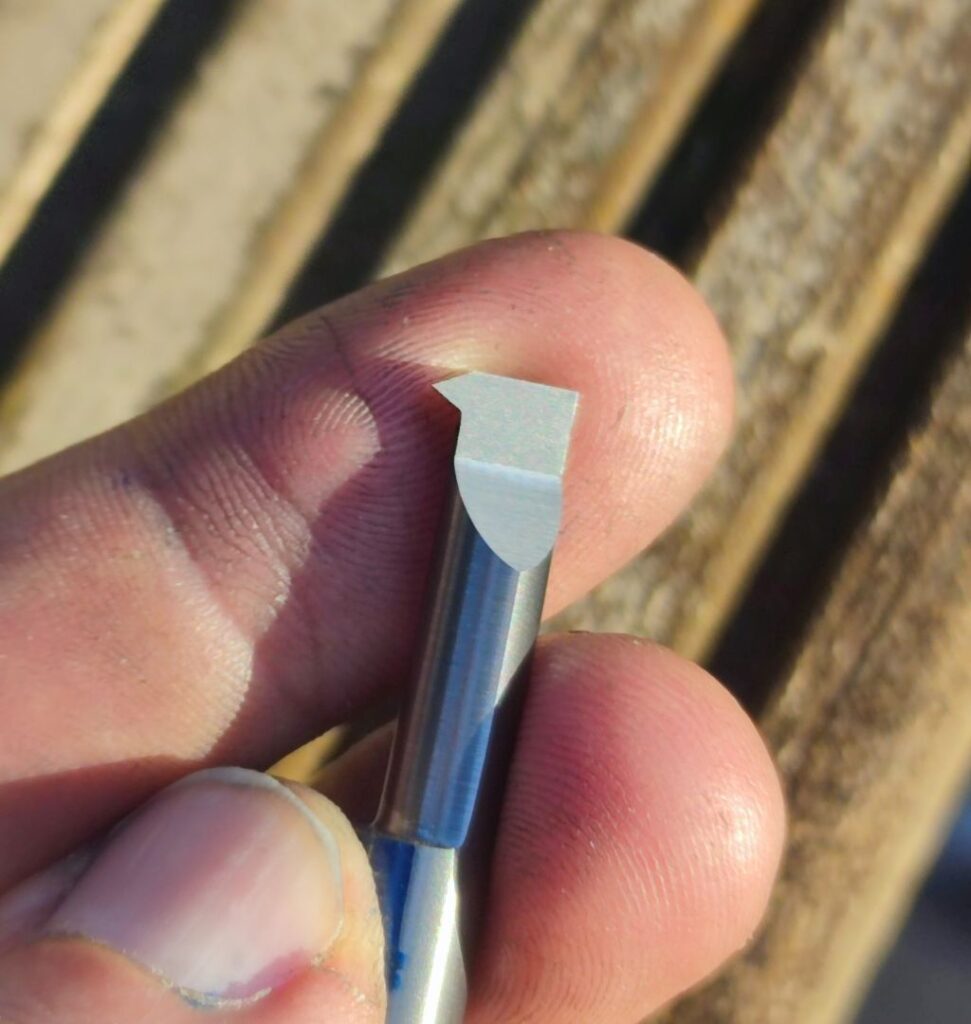
Tool grinding, boring bar
This is an example where a boring bar has been ground from a 8mm solid carbide rod to fit a certain application.
The angle adjustable transfer block is a great addition to the punch grinder, it allows very quick angular settings with having to set a sine plate.
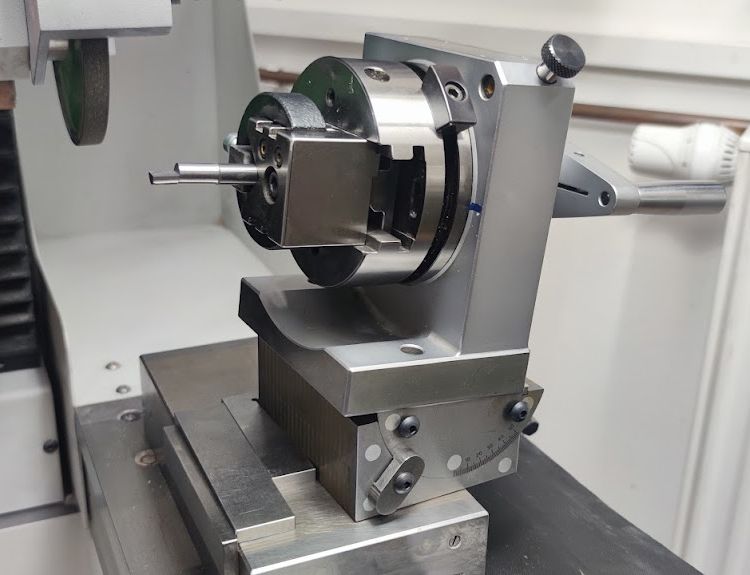
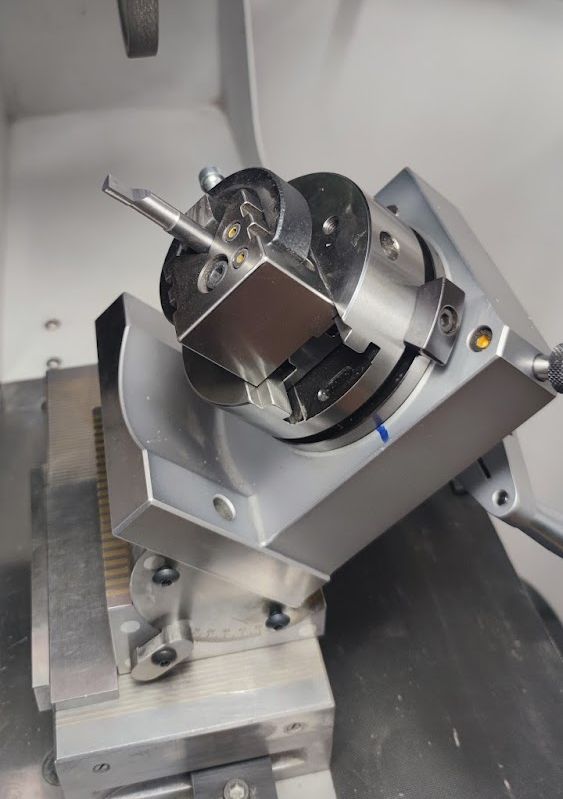
Grinding a custom plug gage / gage pin
Sometimes a custom gage pin is required – Cylindrical grinding out of hardened stock is a very viable option.
Here an old 16mm HSS Endmill is cut down and ground to a diameter of 12.6mm. Note that the V-Block has been removed and a ER25 chuck has been installed instead for clearance reasons (The clamp of the V-Block was interfering with the wheel nut.)
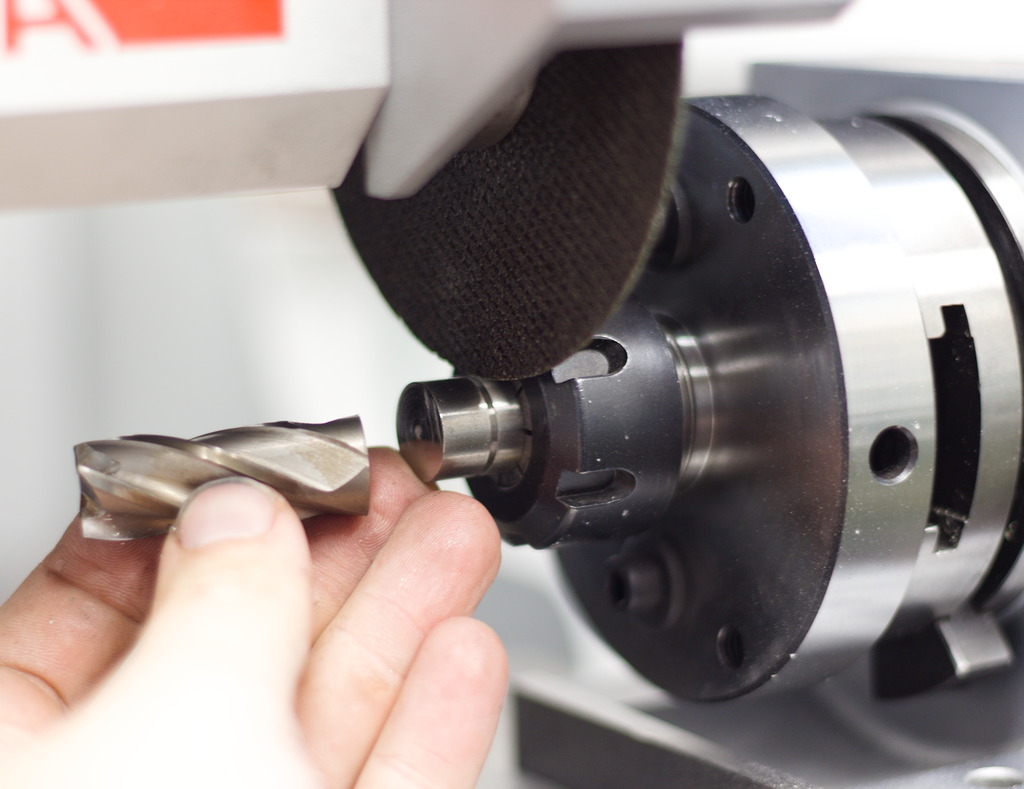
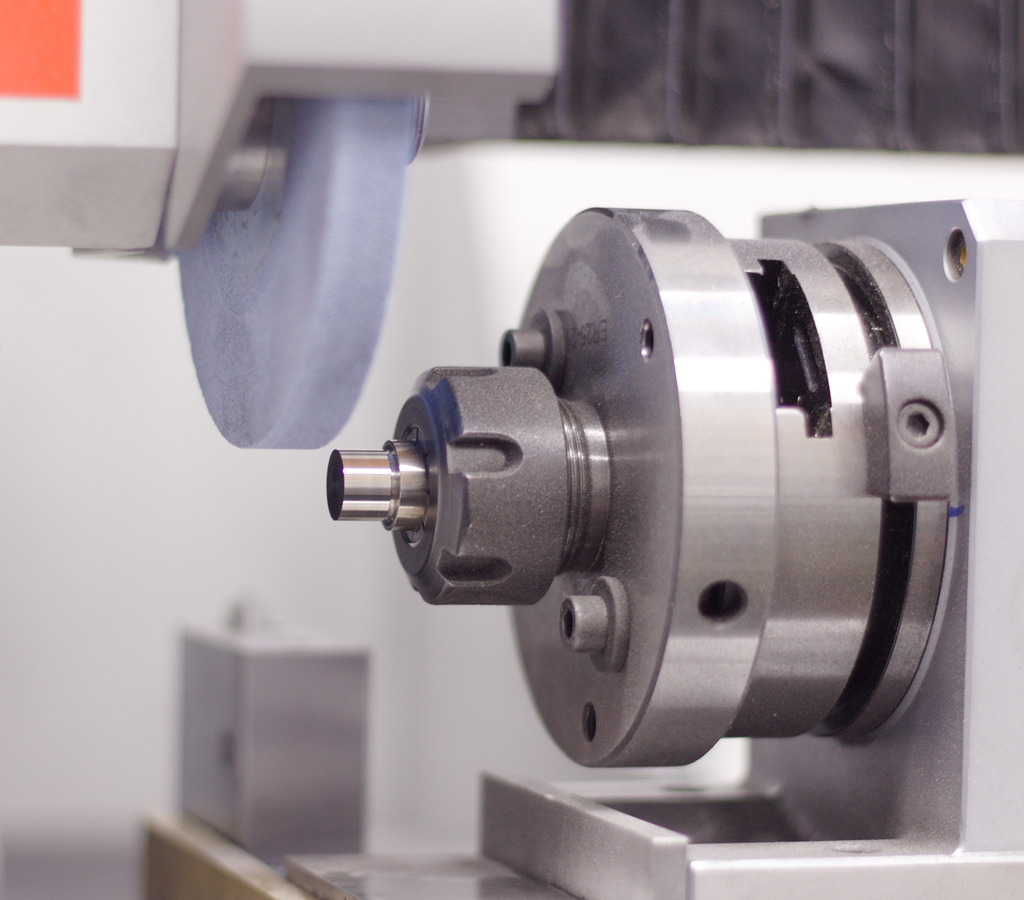
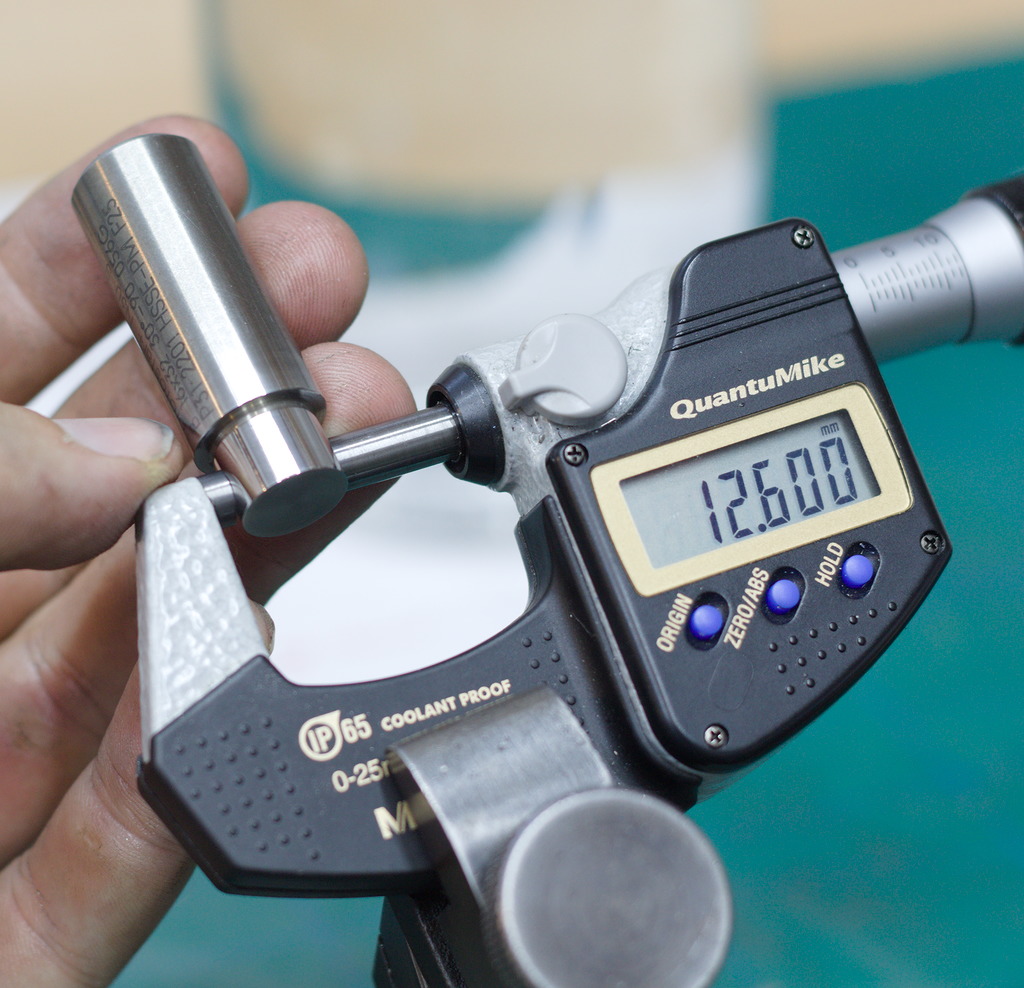
Indexing on the milling machine angular cross holes
For light duty applications, the punch grinder can be used on milling machines as a workholding and indexing tool.
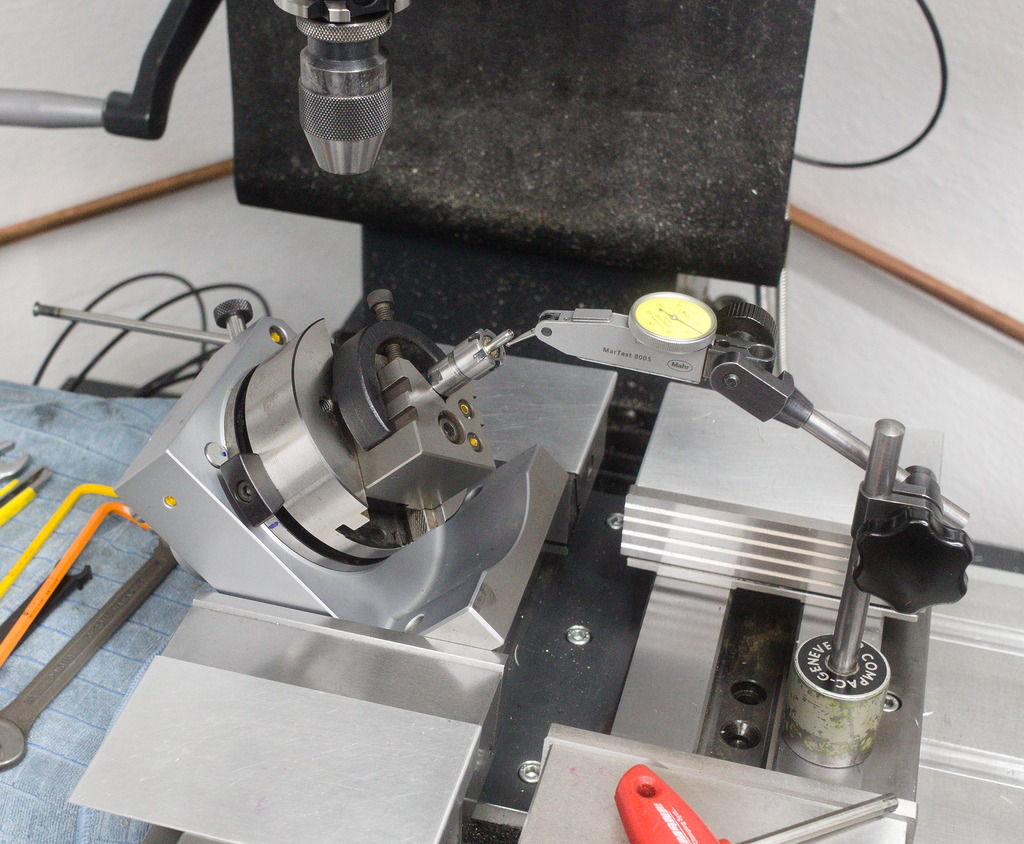
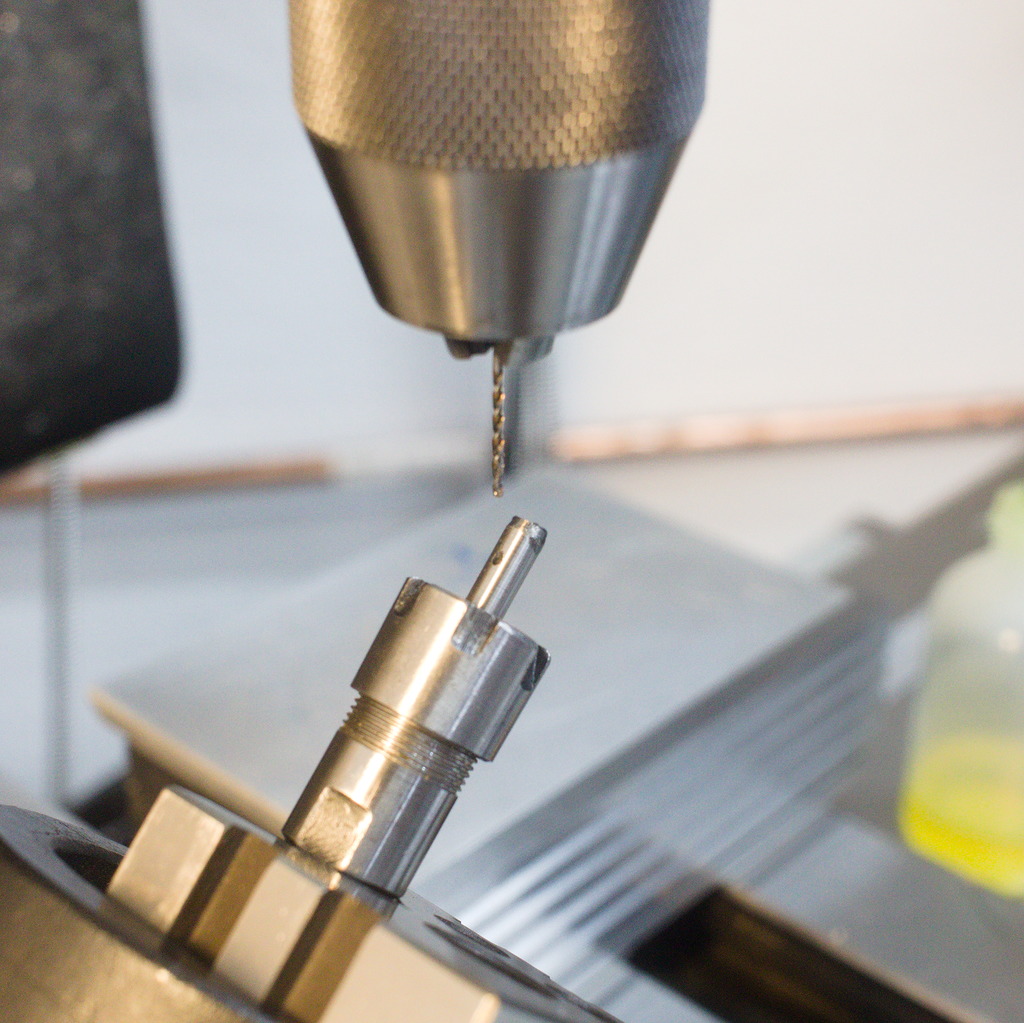
In this case, the punch grinder is held in a vise at an angle, to drill angled holes into a small component.
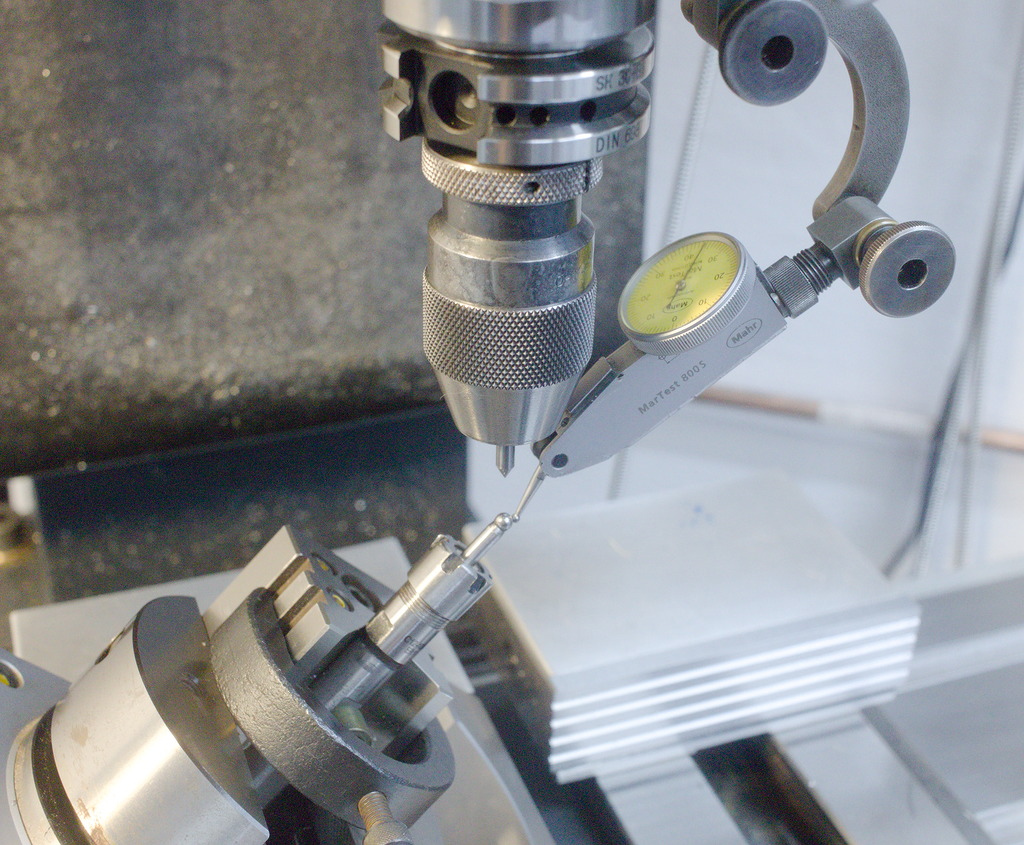
A tooling ball, superglued to the end of the workpiece is used to locate the work.
The workpiece was too short to be held directly in the V-block of the punch grinder, instead a ER11 collet chuck with straight shank is held in the V-block and used to clamp the part.
Adam Demuth provided me with a wealth of pictures for uncommon setups using different spin fixtures – Thank you Adam!
Adam on Youtube: https://www.youtube.com/@adamthemachinist
ID Grinding
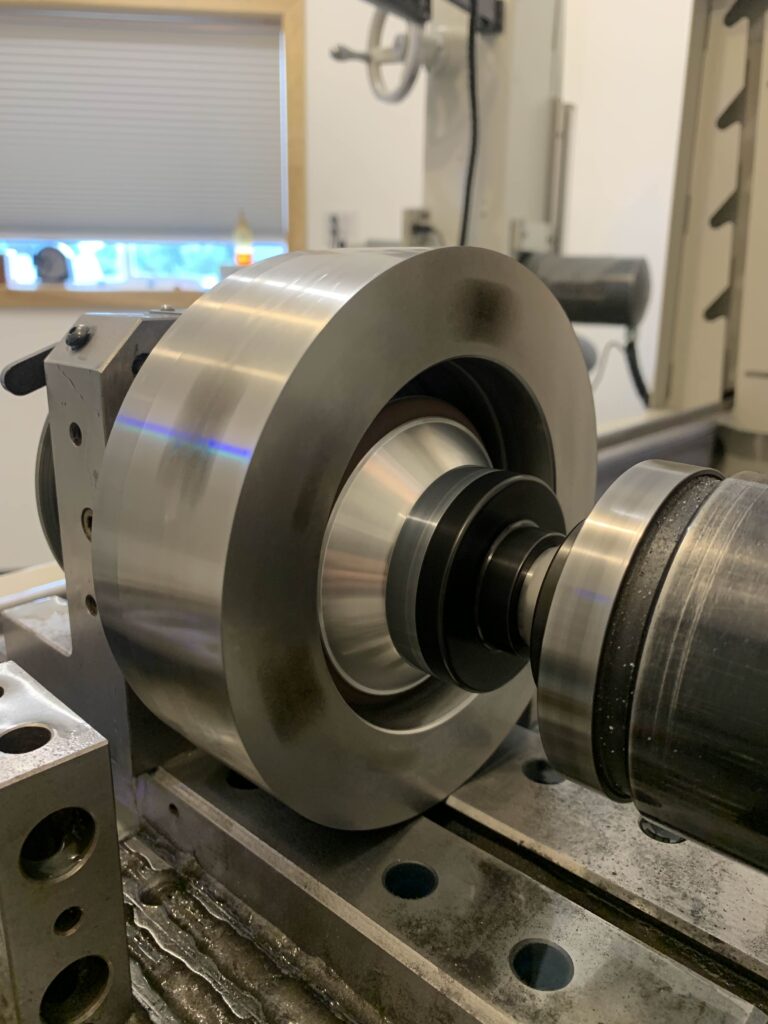
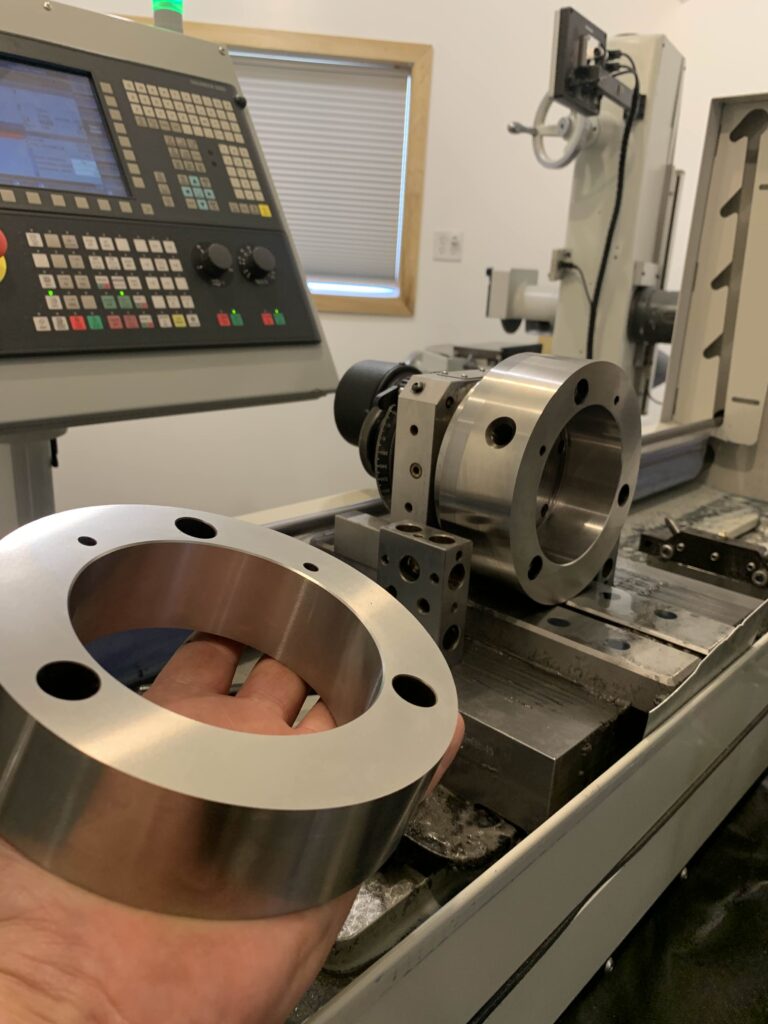
ID grinding a large, hardened ring using a CBN Cup wheel. The work is mounted to a Newbould indexer.
Adam mentioned that the Newbould indexers have a stiffer bearing arrangement than others, which is very helpful in situations with heavy/larger workpieces or large overhangs.
Grinding edge radii on small workpieces
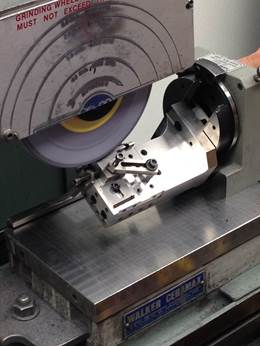
Speaking of large overhangs, this is an interesting fixture to put radii on the edges of workpieces.
Adam mentioned some problems with this setup: The spindle axis of the spin fixtures is not that perfectly aligned with the base of the fixture as we would like, and the large overhang is on the edge of practicability for this Harig Grind All Nr. 1.
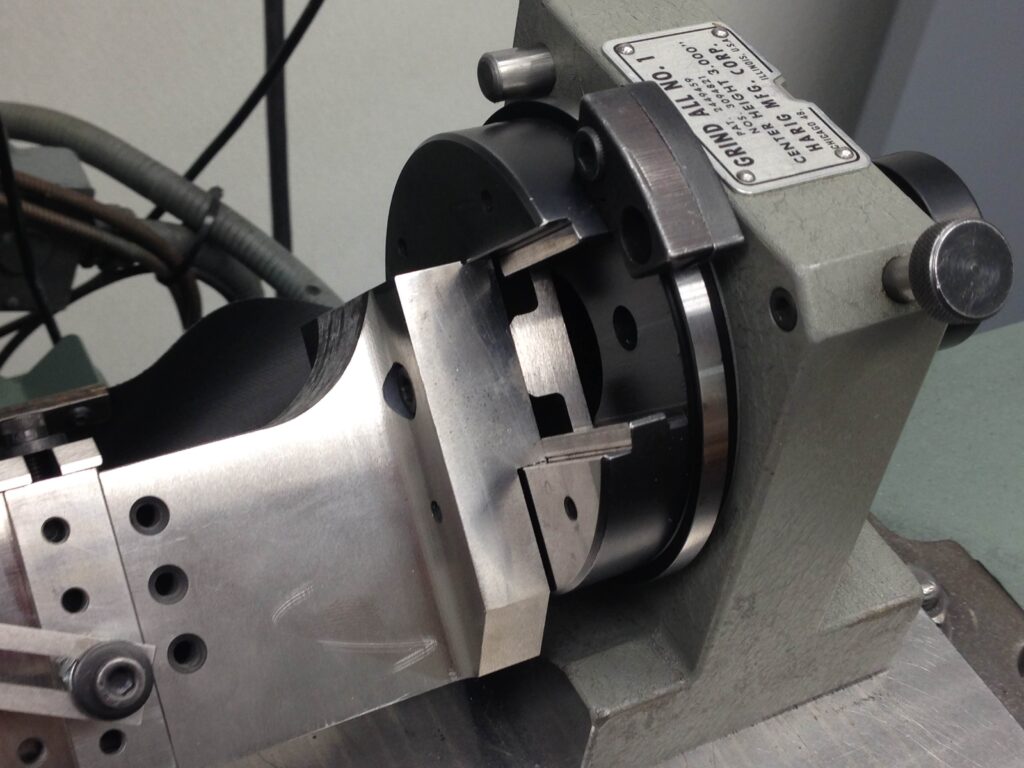
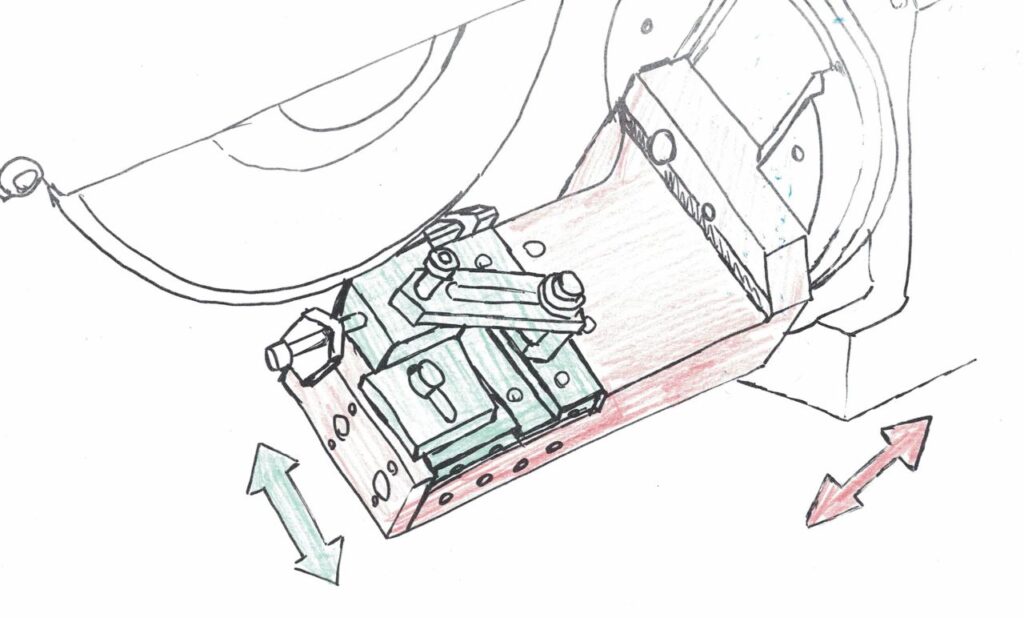
This fixture is mounted on the spin fixture instead of the stock V-Block – Two axis of movement are required to get the corner of the workpiece into the right position.
The first one is sliding the entire fixture in the ground slot of the spin fixture (Red)
The second axis is built into the fixture, by sliding the small block, that’s inset to the fixture, side to side. (Green)
This block has also threaded holes for work holding and work stops.
Using a spin fixture as a bender
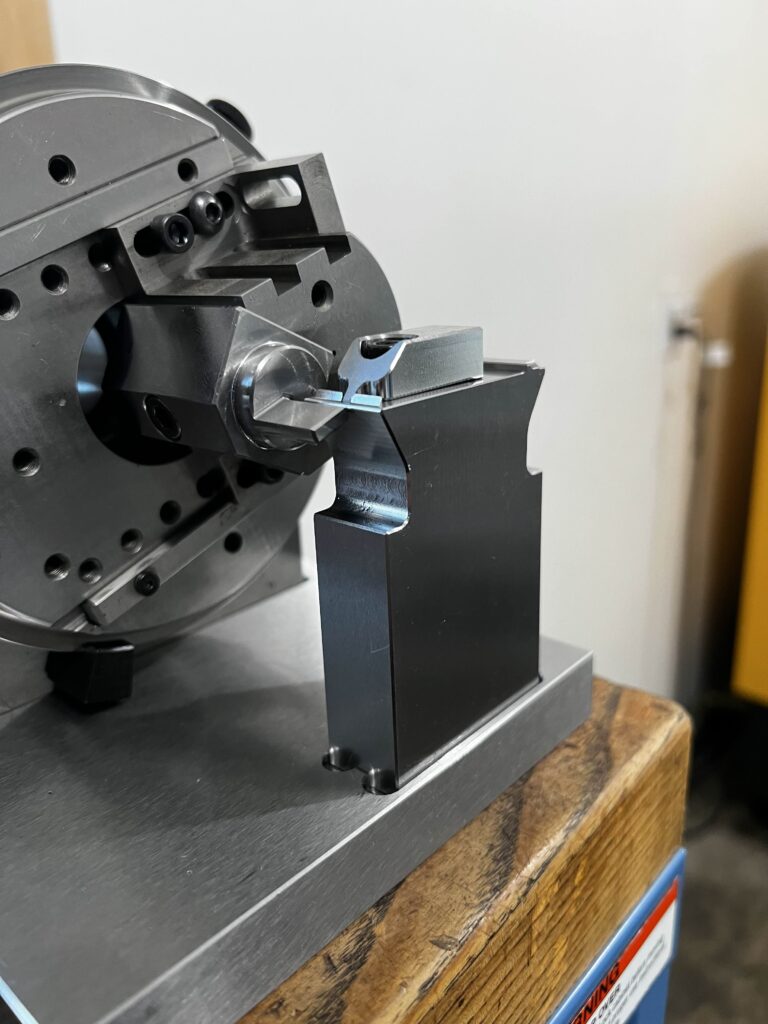
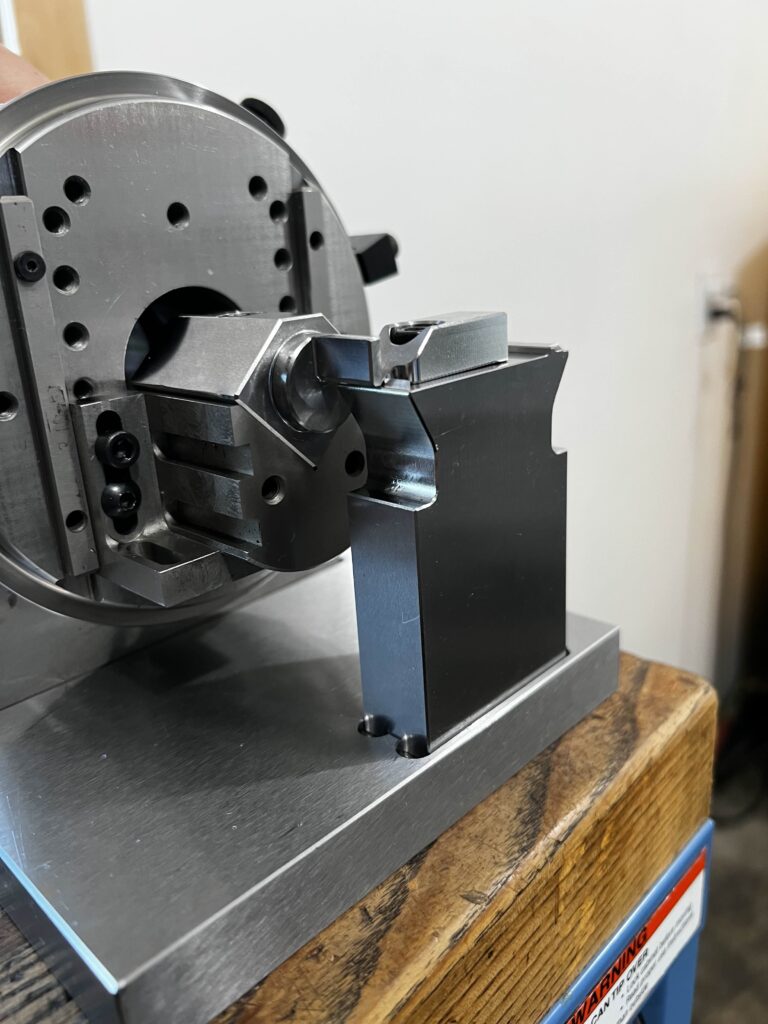
Here the spin fixture is utilized in a very uncommon scenario – As a bending fixture for prototype work.
A bending blade is held in the V-block and a workpiece rest/clamp is mounted on a base plate.
This goes to show the spin fixture has uses outside of grinders/mills/jig grinders too.
ID work on a Jig Grinder
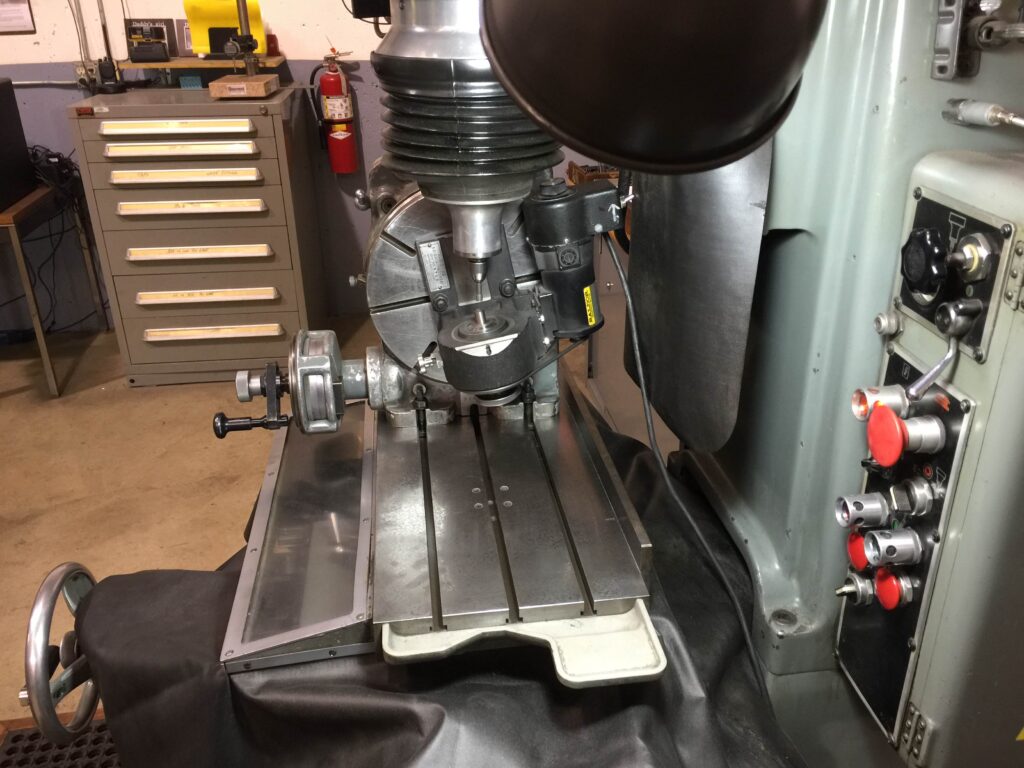
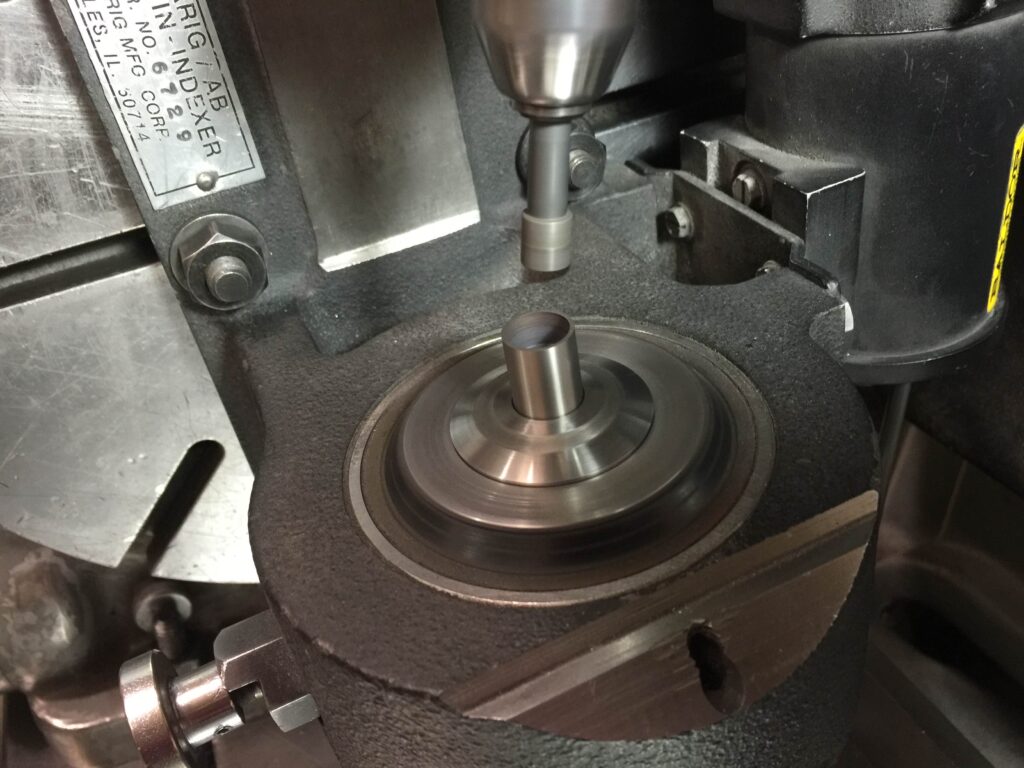
This is an interesting setup – Not with a punch grinder, but a 5C spin fixture, also made by Harig. The principles stay the same, would also work with a punch grinder.
The spin fixture is mounted against a large rotary table to swing it at an angle. This arrangement can be used for tapered ID grinding, grind radii or to, grind radius pockets.
There is a hand full of manufacturers making and selling Spin fixtures:
Harig
Herman Schmidt
https://www.hschmidt.com/areas/spin-indexing
Imperial Newbould
https://www.imperialnewbould.com
Gin Tech
https://www.gin-chan.com/en-US/pfilter1_1_2-punch-formers
Pfeil Magnettechnik
https://pfeil-magnetspanntechnik.de/Stempel-Schleifgeraet-Delphi1
More exist, but thats the common and to me known ones.
Conclusion
All in all, a punch grinder of any form is a great addition to a machine shop – A surface grinder along with one of these devices can solve a lot of problems, replace in a lot of cases a tool and cutter grinder, its useful for metrology purposes or for delicate work on milling machines.